Zerreissprobe am Computer
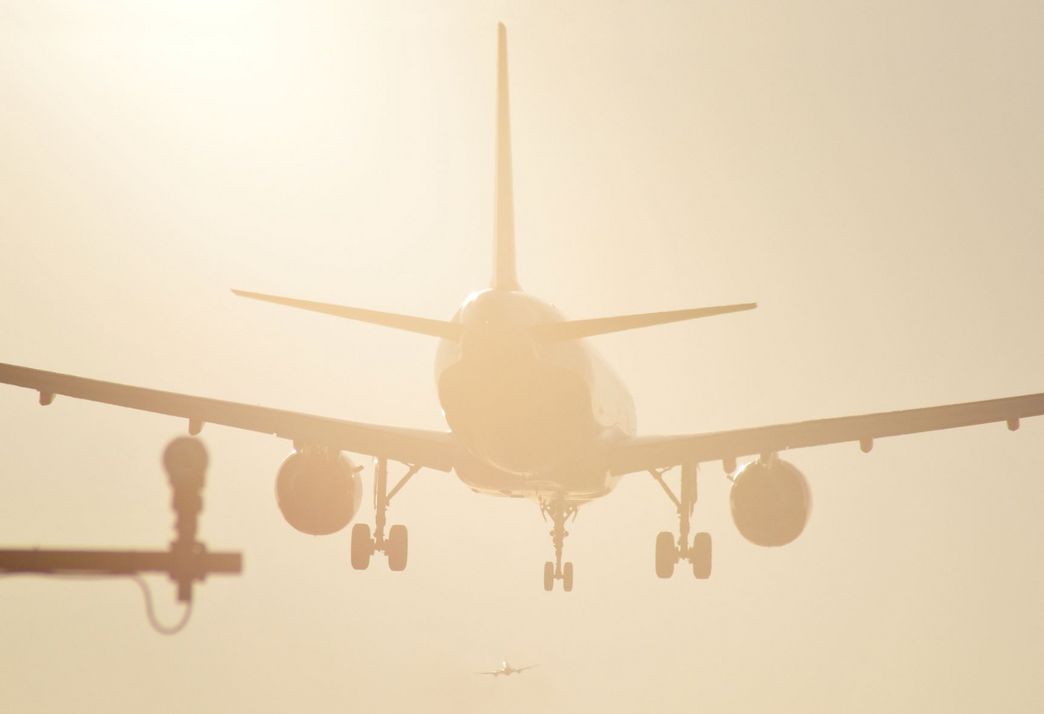
Künstliche Intelligenz erkennt inzwischen Risse im Flugzeugrumpf. Zukünftig soll neben KI aber auch Robotik eingesetzt werden, um komplette Versuchsabläufe bis hin zur Ergebnisauswertung zu automatisieren.
Materialwissenschaftlerinnen und -wissenschaftler des DLR führen deshalb aufwendige Werkstoffuntersuchungen und Experimente durch − von ganzen Komponenten bis hin zu Mikrostrukturen. Sie setzen Bauteile mechanischen Kräften aus, wie sie während des Fluges auftreten, beobachten ihre Reaktion und zeichnen diese mit Kameras auf. So lernen sie deren Grenzen kennen und können das Verhalten verstehen. „Wir wollen die Eigenschaften der Werkstoffe bis an ihr Limit ausnutzen. Wenn wir das kennen, wissen wir, wann das Flugzeug gewartet werden muss, und können die Zeitspanne zwischen Wartungsintervallen besser einschätzen“, sagt Eric Breitbarth und ergänzt: „Das spart Zeit und Kosten.“ Außerdem spart es natürliche Ressourcen, denn letztendlich müssen die schweren, widerstandsfähigen Metalle dann nur dort im Flugzeug verbaut werden, wo sie wirklich benötigt werden. Die Flugzeuge werden entsprechend leichter und verbrauchen weniger Treibstoff. Trotzdem sind sie sicher und können Belastungen wie Windböen oder hohem Kabinendruck standhalten.
Algorithmen spüren Risse auf
Dabei helfen dem Team in der Abteilung Metallische Strukturen und hybride Werkstoffsysteme Methoden der künstlichen Intelligenz (KI). Damit entwickeln sie schneller präzise Werkstoff- und Vorhersagemodelle. Zwei Beispiele sind die digitale Bildkorrelation und das Deep Learning. Bei Ersterem wird über das Bauteil ein virtuelles Bild gelegt. Dieses zeigt an, wo die Belastung im Material hoch und wo sie niedrig ist. Dort, wo die Beanspruchung am stärksten ist, bilden sich über kurz oder lang feine Risse im Metall. Diese Werkstoffermüdung ist ein völlig normales Phänomen im Leben eines Luftfahrzeugs. Werden die Risse zu groß, muss das entsprechende Bauteil bei einem der regelmäßigen Wartungstermine ausgetauscht werden. Der Algorithmus der digitalen Bildkorrelation erkennt diese Risse. Von ihnen lassen sich außerdem Materialkennwerte ableiten. Sobald die Software eine entsprechende Stelle identifiziert hat, wird sie von automatisch nachgeführten Mikroskopen fotografiert. Hierfür entwickelten die Forscher einen intelligenten Auswertealgorithmus. Dieser berechnet, wie sehr die Rissspitze beansprucht wird, und wertet aus, in welchem Stadium sich die Risse befinden. Auf Basis dieser neuen Technologie können die Experten neue Lebensdauermodelle für Materialien erstellen.
Neben den 2D- und 3D-Bilddaten, die durch die digitale Bildkorrelation entstehen, ist es für die Wissenschaftlerinnen und Wissenschaftler unerlässlich, die Mikrostruktur des Gefüges von beanspruchten Flugzeugkomponenten zu kennen. Mit Hilfe einer 3D-Computertomografie erstellen sie dafür ein virtuelles Abbild des Werkstoffs. In dieser Aufnahme sind seine einzelnen Bestandteile gut zu sehen. Mussten die DLR-Wissenschaftlerinnen und -Wissenschaftler diese Abbilder bisher in zeitaufwendiger Arbeit manuell auswerten, so übernehmen heute erste trainierte Deep-Learning-Algorithmen diese Arbeit. Die Software ermittelt und bewertet die Zusammensetzung des Materials in einem Bruchteil der Zeit. Am DLR-Institut für Werkstoff-Forschung werden die Verfahren des maschinellen Lernens und insbesondere der Convolutional Neuronal Networks (CNN) mittlerweile sehr erfolgreich zur Mustererkennung und semantischen Bildsegmentierung eingesetzt. Dies trägt dazu bei, große Datenmengen der Computertomografie schnell und präzise auszuwerten und liefert somit Einblicke, die mit herkömmlichen Methoden nicht zu erfassen sind, beispielsweise in den Schädigungsprozess im Bauteilinneren.
Testen bis ans Limit
Getestet werden die Materialien an einer biaxialen Prüfeinrichtung im Institut für Werkstoff-Forschung in Köln. An dieser werden die Proben mit Hilfe von vier Hydraulikzylindern in zwei Richtungen belastet und bis zum Bersten gespannt. So kann im Experiment die Belastung auf den Flugzeugrumpf während der bis zu mehrere Jahrzehnte währenden Lebensdauer innerhalb weniger Stunden abgebildet werden. „Die Anlage ist bei uns schon länger im Betrieb, aber die KI eröffnet uns völlig neue Möglichkeiten“, freut sich Eric Breitbarth. So soll zukünftig neben KI auch Robotik eingesetzt werden, um den kompletten Versuchsablauf bis hin zur Ergebnisauswertung zu automatisieren.
Text: Dr. Frank Seidler, verantwortlich für Marketing und Kommunikation am DLR-Institut für Werkstoff-Forschung
Dieser Artikel ist zuerst im DLR-Magazin 163 erschienen.